Vacuum deposition
Vacuum deposition is a film formation technology that heats the vapor deposition materials in a vacuum to convert them into a vapor through evaporation and sublimation, and then forms a thin film when that vapor adheres to the substrate. The method for heating the material may be electron beam heating or resistance wire heating. Although it is a conventional film formation method, its characteristics include that it can be used for substances that easily become detached, such as fluoride, and that it is possible to form films at a high film formation speed. It is also possible to select from a wide range of materials, so it can be applied to a wide range of products. It is suitable for use in the production of items such as ultraviolet region filter products and laser optical elements.
▼ Equipment overview diagram
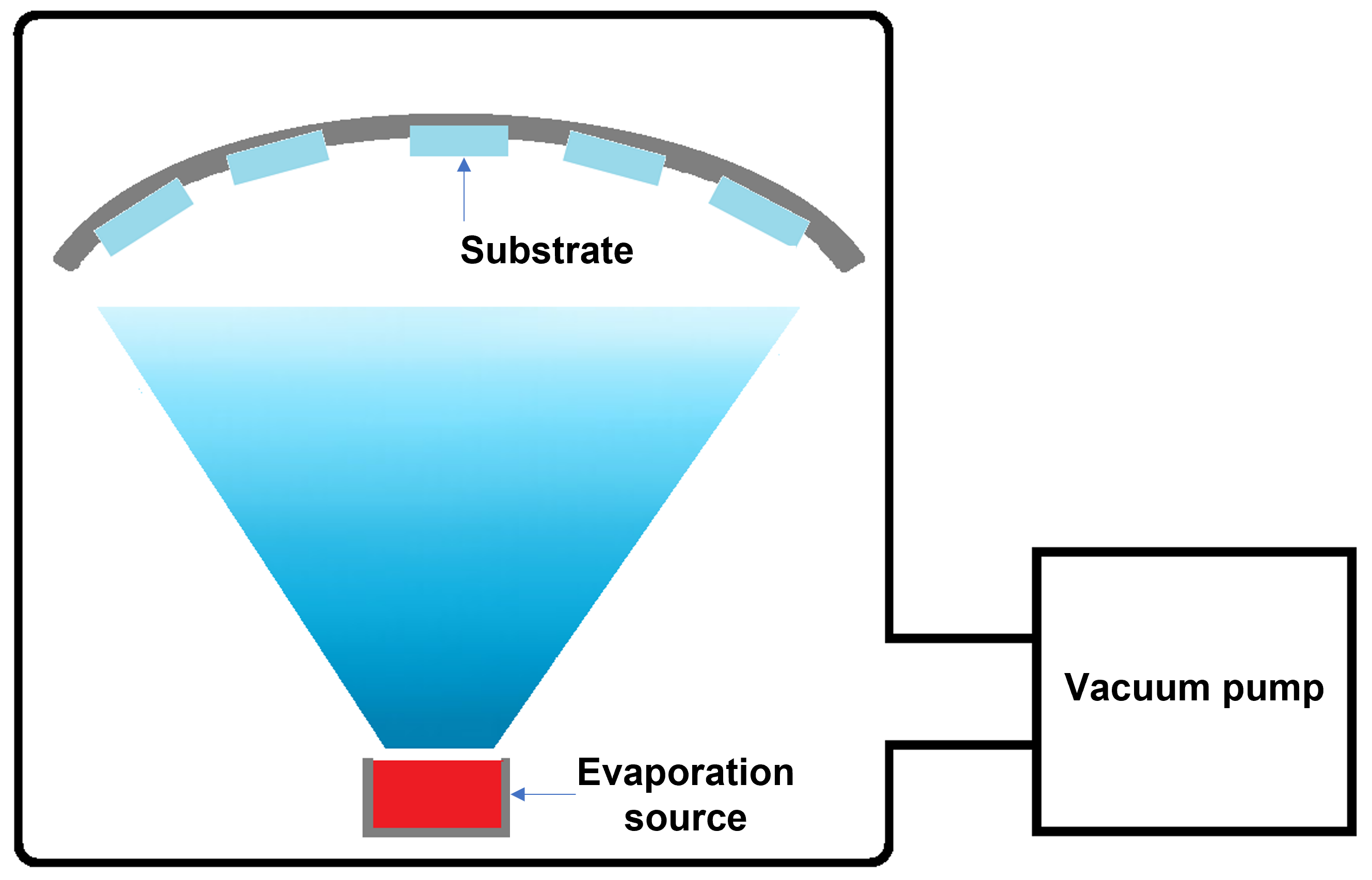
Materials: SiO2, Ta2O5, HfO2, ZrO2, TiO2, Al2O3, ZnS, ITO, SiO, Na3AlF6, MgF2, GdF3, LaF3, YF3, YbF3, CeO, Au, Ag, Al, Cr, Ni, etc.
Substrates: Various types of glass, quartz, sapphire, germanium, silicon, chalcogenide glass, etc.
(Please contact us if you have any requests for materials other than the above.)
Ion beam sputtering
Sputtering is a process in which the material to be sputtered and form the film (the target) is bombarded with Ar+ or other ions and atoms in a plasma state. This ejects particles out of the target and they form a film on the substrate. Compared to vacuum deposition, where the target material is heated to evaporate it and form a film, ion beam sputtering gives the target molecules higher energy, so the film has a stronger adhesion strength and it is possible to form a denser film. Ion beam sputtering uses a sputtering source called an ion gun. A high frequency (13.56 MHz) is applied to argon gas to turn the gas into plasma. Argon ions are extracted from the generated plasma by applying a voltage to a part called a grid. The extracted argon ions collide with the target material and sputter the film material. It is possible to form multilayered optical films by depositing the sputtered film material onto a substrate. The features of ion beam sputtered films are that they have few defects, low loss, high smoothness, and can be formed in low temperature deposition.
Substrate sizes supported: Up to φ 200 mm
Materials: SiO2, Ta2O5, Nb2O5, HfO2, Al2O3, etc.
Substrates: Quartz, glass, fiber end face, crystalline material, etc.
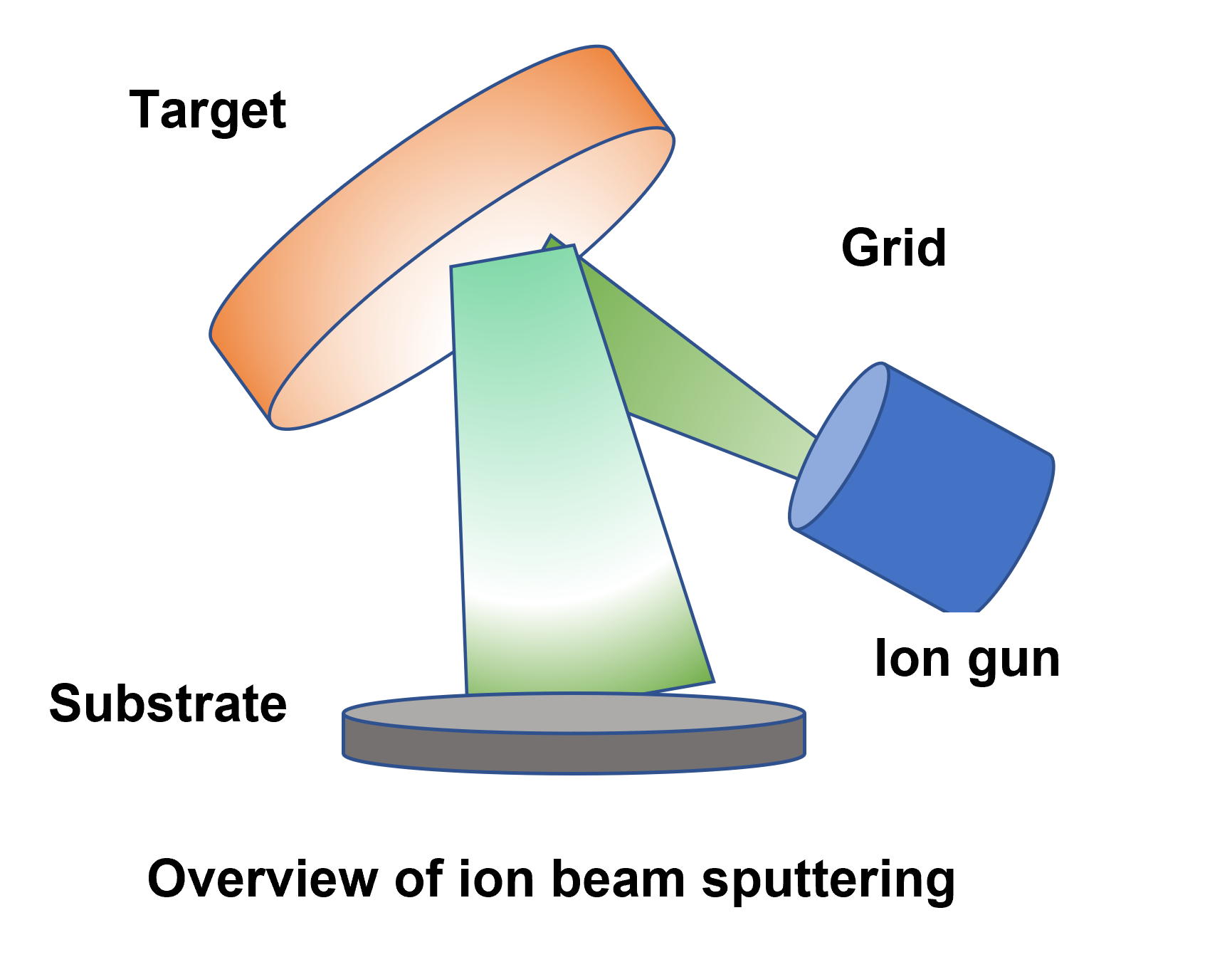
Magnetron sputtering
Sputtering is a process in which the material to be sputtered and form the film (the target) is bombarded with Ar+ or other ions and atoms in a plasma state. This ejects particles out of the target and they form a film on the substrate. Compared to vacuum deposition, where the target material is heated to evaporate it and form a film, ion beam sputtering gives the target molecules higher energy, so the film has a stronger adhesion strength and it is possible to form a denser film. In magnetron sputtering, a magnet is placed behind the target to generate a magnetic field so that electrons are enclosed within the field. This creates areas of dense plasma that make it possible to sputter the target efficiently. Unlike vapor deposition, where the deposition source is a point, magnetron sputtering makes it possible to form a uniform film over a large surface area.
Materials: SiO2, Ta2O5, Nb2O5, etc.
Substrate: Glass, quartz, sapphire, silicon, etc.
▼Equipment overview diagram
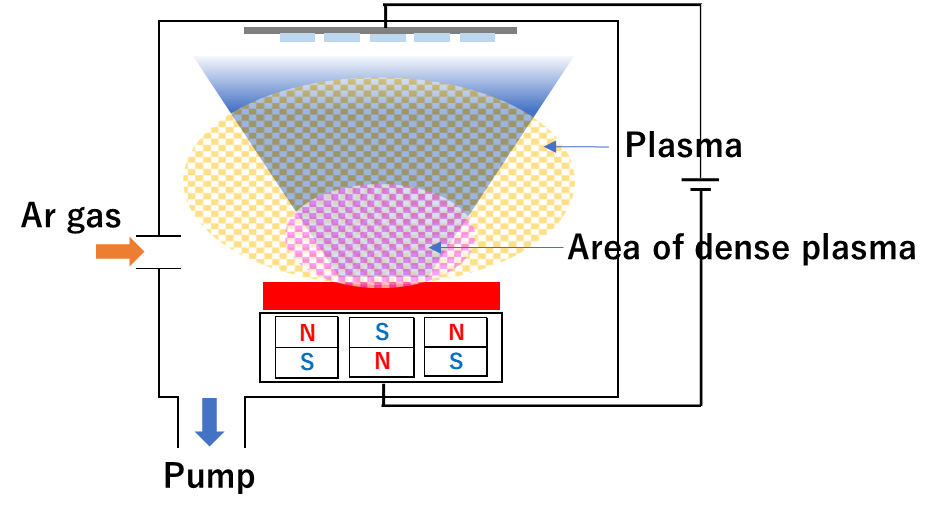